Electronic Trace Detection (ETD) Equipment Replacement
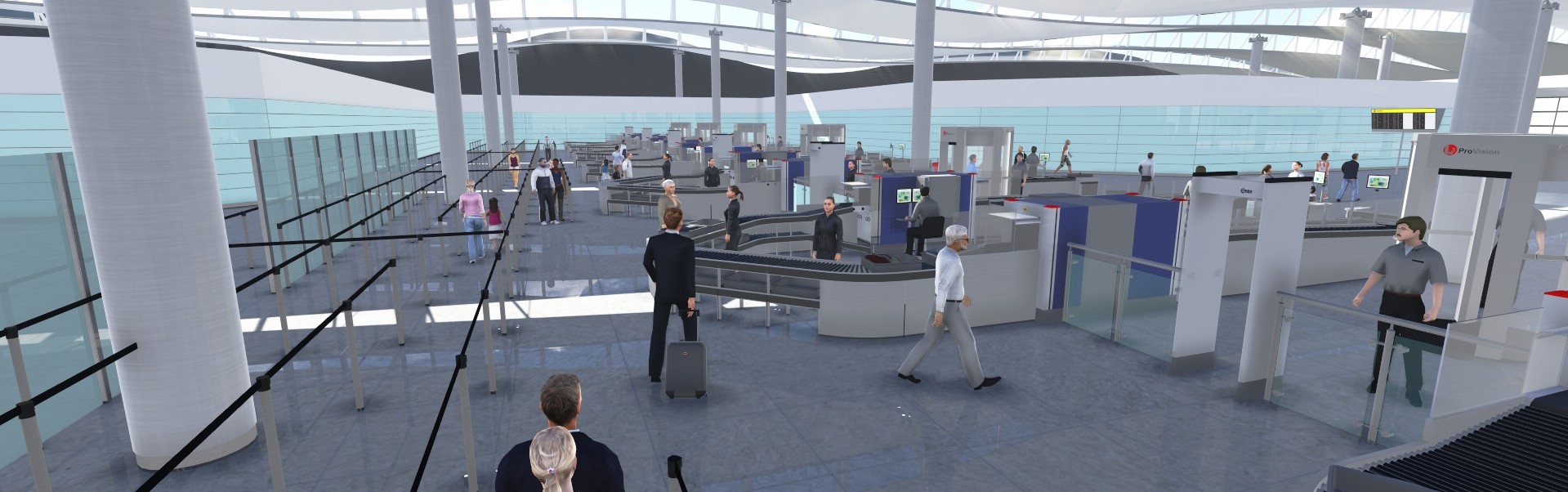
The challenge
Explosive trace detection (ETD) systems are used to identify the presence of explosives by detecting trace amounts in the form of particulate material or vapour. ETD is an indispensable part of airport security screening and is utilised in a number of regulated screening situations at airports.
In anticipation of pending regulatory changes in 2020, Heathrow Security and Engineering teams have a requirement to identify the best ETD solution for Heathrow, airport-wide, to inform a replacement strategy for its current ETD equipment.
Following on from a recent equipment evaluation and implementation project relating to liquid explosive detection systems which was led by o&i consulting, Heathrow Airport Ltd (HAL) asked our team to help to identify the optimum type and amount of ETD equipment required by the airport by conducting a series of offline and live operational trials of available ETD technology, assessing the equipment for operational performance and usability (including networking capabilities), activation rate and reliability.
Our role
Commissioned to lead the end-to-end ETD product trial and selection process for all airport security operations at Heathrow which use ETD technology, o&i collaborated with internal and external stakeholders, ensuring they were engaged and informed throughout the project. We worked closely with terminal operations and management teams to encourage ongoing, open communications including verbal and written briefings, regular working and steering group sessions, and officer feedback and input.
Identifying all available ECAC certified and DfT approved equipment, our team communicated with ETD equipment manufacturers to develop a good understanding of their technology and identify the most suitable products to trial based on HAL requirements. For the selected equipment, we worked with the suppliers and Heathrow terminal operations teams to deliver and install the trial equipment, ensure that all appropriate performance and emissions testing was performed, and complete the necessary operational training prior to the start of the trials.
Before introducing the trial equipment into live operations, o&i carried out a series of “head to head” off-line trials to generate baseline performance data and to ensure that any equipment introduced into the live operation was suitably robust and performed sufficiently well so as not to disrupt business as usual operations. Each product was then trialled in live operation over a number of weeks. This provided the opportunity to evaluate the technology in terms of operational use, maintenance and reliability, commercial impact, and number of machines required, amongst other measures. Relevant information was collected during the trials to enable us to directly compare the machines.
o&i’s operational research (OR) team performed in-depth analysis of the results of the trial and produced an individual assessment of each machine’s performance as well as ranking and rating the overall trial equipment based on both qualitative and quantitative findings. From these results, a shortlist of products was identified. These technologies were subjected to further live “extended reliability” trials, where they became embedded in the screening operation and their performance analysed on a weekly basis.
The performance based assessment from the trials, feedback from users (Operations, Engineering and other key stakeholders), further communications with equipment manufacturers, and a detailed assessment of product life cycle costs were used to inform the tender process and support the procurement team.
o&i consulting continues to work with HAL to determine and integrate the agreed ETD solution.
“This project was carried out over a period of almost one year and required engagement with both internal and external stakeholders. The communication and reports received from o&i throughout the assignment was meticulous. It provided Heathrow with the required data to create and submit a tender to those manufacturers of ETD equipment, who exceeded the performance requirements set out in the brief that was developed between LHR and o&i.
From my experience of working with o&i, I can unconditionally recommend the services they offer.”
Paul Evans, Systems Engineer, Heathrow Airport Ltd
o&i expertise
- Product research
- Stakeholder engagement and coordination
- Communications
- Trial set up and management
- Data analysis and modelling
- Equipment evaluation and recommendation
- Tender process support and independent advice
- Process engineering and optimisation
- Aviation operations expertise
- Reporting and presentation
Project Key Facts
Title: Electronic Trace Detection (ETD) Equipment Replacement
Client: Heathrow
Theme: Passenger Security Screening